When a company decides to implement manufacturing intelligence (MI), the goal is a successful long lived project that delivers manufacturing decision support and an ongoing ROI. The question becomes how to identify a dependable, systematic way to guarantee a successful MI implementation.
Research shows companies spend $50B to $80B dollars on failed IT projects each year. One top reason in the studies is the project fails to achieve the expected business value.
System technology is usually not the only reason for failing to make targets, and managing technology deployment alone is not enough. Success depends also on developing and managing the operational routines which will use the technology.
Ever since the Hawthorne Effect was identified at Western Electric, companies have observed projects that initially improved performance but then dropped off. If the company is lucky, the resulting performance is at least above the original starting point. The next project takes off from that level until it in turn decays back to a lower level (figure 1). Throughout these cycles the sustained gains are insufficient for a good ROI.
If on the other hand, the project is properly implemented and gains are maintained, the next generation of process improvement can begin from the higher level of performance (figure 2). This path leads to world-class performance.
A total-system approach – combining the technology with developing the organization’s people skills – is critical to implementing sustainable manufacturing management and MI systems. The most effective methods rely on established standards such as the Deming PDCA cycle – Plan, Do, Check, Act.
The variant, Discover, Align, Enable and Sustain, provides a path to success. This systematic approach develops a management program that seamlessly aligns technology, people and processes and uses MI to transform the company into a high-performance, knowledge-driven organization. The individual elements of Discover, Align, Enable and Sustain make this feasible.
Discover
The goal is to understand the project scope and develop measures for success. Best practice is to follow ISA95 standards and align metrics across the organization. As with all successful quality and process improvement programs it is wisest to identify the quick hit projects to build organizational engagement.
By thoroughly analyzing operations and systems the company can successfully develop systems that insure desired improvements are actually incorporated into the organizational fabric.
In the discovery phase the project group examines:
- Business technology needs
- Metrics alignment
- Technology capability
- Management control systems
- Quantifiable opportunities for improvement
Align
The goal is to develop a change mandate and design systems that align with the mandate and resonate with the people. The discovery process enables teams to develop a management system that seamlessly aligns People, Process, and Technologies.
Proper alignment process creates a consistent system that:
- Exactly fits the capabilities and needs of each stakeholder;
- Increases the potential effectiveness of each person and piece of equipment;
- By creating a path of least resistance improves the chance of long term success.
This generates improved management insight while sustaining greater accountability, advocacy and efficiency across the team.
Enable
The goal is to deploy systems so that people understand their role in management systems and drive accountability for realizing improvement. The team identifies the actionable data so that the project group can work seamlessly with operational management systems to insure the delivery of the right information to the right people at the right time.
This project creates:
- The informational infrastructure for consistently better decision making;
- Easy, immediate access to knowledge bases of enterprise experience;
- The means to contribute to the evolving knowledge base and continuously improve enterprise operational capabilities.
Sustain
The goal is to deploy processes that consistently assess and reinforce the management system thereby insuring that the value of MI is realized over time. Implementing a system of processes, training vehicles, audits and advocacy creates a sustainable and transferable program for the continued optimization of your manufacturing operation.
These steps create the foundation of a sustainable and transferable program for the continued optimization of your manufacturing operation. They enable the staff to be actively engaged in the transformation of the company into a high-performance, knowledge-driven organization.
The right focus and balance of people, process, and technology enables the project group to reach the performance sweet spot and deliver a successful implementation (figure 3). Each successful element exhibits these properties:
- Process focused
- Proven value with the right client
- Leverages technology to drive sustained value
- Provides the means to open managerial conversations on a consistent basis
Quality products are the desired end result. To get there the system needs to define the production process, the SOPs, and the metrics and KPIs which characterize process performance. Ideally, staff at all levels is brought into the definition process. Then the staff must be trained to the operational standards and the support programs of auditing the standards and corrective actions implemented. The entire process treats the specific technology system as the operational infrastructure. That technology is critical but not functional unless the overlying corporate processes and staff capabilities have been developed and are in place (figure 4).
Summary
The common industrial temptation is to focus on the “easy” engineering part of management systems while deferring the more difficult people part of incorporating the system into the daily work life. However, the organizational and workforce issues need the same level of attention if successful and sustainable manufacturing management systems are to be developed.
The system needs to be easy to use and embedded in company culture to survive time and employee turnover. This is not just for internal needs, but also to meet commercial standards such as ISO 9001:2008 and ISO 22000, both of which demand systems that are sustainable from one audit to the next.
MI becomes a significant part of the corporate infrastructure. It delivers the role-specific reporting that empowers each person to successfully do their job in the context of enterprise goals. The winning strategy for MI actively combines easy-to-use and easy-to-implement technology with people skill development.
The expected results for a properly designed and implemented system are:
- Break the cycle of limited results to increase ROI and sustain results;
- Effectively engage all capable resources from executive management through line operators;
- Provide a definition of success for all levels of the organization;
- Develop management systems that sustain these goals through:
- Accountability;
- Standards;
- Documented processes.
This brief overview indicates what is possible by taking an integrated approach to technology, people and process to develop a sustainable and effective MI system. This discussion is based upon the webinar presented by Rob Bansek, SightBridge Consulting, “System Implementation for EMI – Go Live is Just Another Milestone”, which provides an in depth examination of the process.
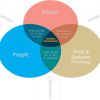