The UK’s largest manufacturer of plasterboard and dry lining systems uses NWA Quality Information System™ to implement consistent quality processes and improved productivity in plants throughout the UK.
Plasterboard is an unsung hero of the modern construction industry. By replacing wet plaster wall rendering with dry wall lining systems, builders reduce labor input and, as other work can continue as soon as the plasterboard is installed, they achieve valuable reductions in time on site.
It is no surprise, therefore, that plasterboard manufacturing is big business. British Gypsum is the UK’s largest plaster, plasterboard and related products manufacturer. The company has been making plasterboard for over a century and today produces over 150 million square meters every year in five plants across the UK.
Plasterboard is produced in an extrusion process. Plaster, water and various other additives are combined in a mechanical mixer and extruded between two layers of paper liner, before passing into a forming station which sets the width and thickness of the finished board. The board sets as it passes along the manufacturing line before passing into huge driers that drive off any remaining moisture in the board. It is then cut to length before being distributed to construction projects around the country.
Consistent quality is of critical importance to British Gypsum. Plasterboard products are manufactured to meet European standards which include strict dimensional tolerance limits. The company also has its own internal quality standards, which help to maintain the excellent reputation of its products in the marketplace.
Quality is maintained at the line side through a rigorous batch sampling process. Every three hours, a sample board is removed from the line to undergo a series of up to 40 different tests. These include overall dimensions and a number of checks to meet additional quality standards including the occurrence of voids in the board and the quality of lining paper adhesion.
If a sample board fails any of the line side checks, a prescribed sequence of checks is completed on the rest of the boards in the batch. Boards that fail these secondary tests are recycled; those within tolerance are put back into the supply chain.
Previously the five different British Gypsum board-producing plants, while they all used the same quality checks, had different methods for recording the results. Most used paper-based recording systems of different types, while one had built its own in-house database system.
According to Amanda Nurcombe, Company Quality Systems Manager at British Gypsum, the company wanted to introduce a standard process across all its plants, and to move away from the development and support of in-house software.
After evaluating various products, British Gypsum decided on NWA Quality Information System. NWA QIS is a powerful dedicated solution for plant floor data collection and SPC. The package allows standardized workflow processes to be built to match the needs of a specific production line, stores data from multiple workstations in a central database and provides live charting and analysis of quality data.
British Gypsum installed a pilot NWA QIS at the Company’s Kirkby Thore plant in Cumbria. The ability to customize workflows was an important part of this pilot program, explains Amanda. “Different boards require different sets of tests. With the new system, the operator enters six digits from the manufacturing code that is printed on every board into the first screen of the system, and then NWA QIS pulls up a template with only the required tests on it.”
The NWA QIS software also contains a comprehensive database of acceptable tolerances. As data is entered, the package gives instant feedback if a dimension is out of tolerance and tells the operator which secondary measurements should be carried out. Other optional screens give further support to operators, providing reminders of correct measurement protocols if required.
As well as providing live feedback on measurements, NWA QIS also helps to enforce consistency in all checks. The system will not allow operators to pass a board until all measurements have been made and internal checks require data to be entered in a correct consistent format.
While the line-side benefits of NWA QIS system are immediate, much of the system comes into effect away from the production line. All collected data is linked live to a central database at British Gypsum’s headquarters in East Leake, Leicestershire, while local caches keep data safe in the unlikely event of a network failure.
Production and quality engineers can access this data and use NWA QIS to check ongoing performance, spot trends and search for the root cause of any problems. “Even during the pilot phase, I was able to analyze data at my desk,” explains Amanda. “Now we can compare performance on different products and share best practices between plants.”
For Amanda, who is responsible for ensuring that British Gypsum continues to evolve and improve its quality processes, having a single standard system in place helps greatly with control and flexibility. “With NWA QIS I know that, as our requirements change in the future, the system is flexible enough for us to incorporate those changes directly into the database.”
Update: July 1, 2013
British Gypsum’s plaster and plasterboard plant in Kirkby Thore, Cumbria has been given silver World Class Manufacturing (WCM) status.
The plant achieved an impressive 62 points to earn the WCM silver award during a recent review, which was carried out by representatives from global parent company, Saint-Gobain.
The scheme uses a points-based system to excellence in World Class Manufacturing. The process reviews a range of best practice standards on a global scale, including safety, the environment, plant and customer service performance, process stability and product quality. The WCM qualification process involves three intermediate levels: bronze, silver and gold. After completing these, sites can then go on to achieve World Class Standard.
British Gypsum’s Kirkby Thore site, was presented the silver award for creating a safe working environment for employees and for its commitment to continuous improvement across all areas. The assessors were also impressed with its production processes and focus on environmental performance and energy reduction.
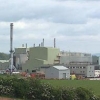