Praxair Electronics produces process and precursor gases used by the majority of semiconductor chip and solar cell manufacturers. The Praxair product line includes ammonia, silane, dichlorosilane, arsine, phospine dopant mixtures, inert gases, halocarbon etchant gases, and support products and services.
Gas contamination and variation affect chip yield rates and the required reduction in impurity levels for successful chip production. Continuous Process Improvement (CPI) drives performance to meet the requirements. To meet their CPI goals, Praxair uses NWA Quality Analyst to drive control limits tighter and decrease variation.
As one of the top players in semiconductor industry gases and related services, Praxair ships high purity gas cylinders around the world to its customers. The data-management system at the Kingman, AZ plant was used as the benchmark model to apply the same methods to ramping up the Quality Analyst systems at other Praxair gas plants in Oevel, Belgium; Giheung and Tangjung, Korea; and Toufen, Taiwan. This global effort has resulted in highly successful customer retention and expanded global business. Praxair is dealing with over 7,000 products and tracking from one to twelve quality parameters per product.
Business requirements are driving the move to less variation and higher process capability. Many customers are demanding tighter process control and "ship-to-control" capability. Vendors such as Praxair who actively use SPC and CPI can successfully negotiate specifications with regard to their actual process capability and guarantee they will be a capable supplier. Their production is at least three sigma level, and with the ongoing CPI program they have projects in place to improve process capability to meet the evolving business demands.
Praxair has automated the statistical queries and reporting. Previously, quality assurance managers spent most of their time compiling quarterly reports for both internal and customer use. Now that it is automated, the staff can hit a button and two hours later, they have generated a comprehensive, multipage report for the customer.
This process has not only eliminated many hours of work, it has substantially reduced variation and errors in the reports. Praxair estimates that not only have they saved one full-time-equivalent salary and overhead, they have freed up the Quality Manager to actively lead CPI efforts rather than just produce charts to monitor the process.
In the lab, they have interfaced 45 instruments to automatically generate results that are passed into an Oracle database where they are used to generate Certificates of Analysis (COAs) and Electronic Data Interchange (EDI). Most customer electronic systems are set up to automatically decline or accept the lots based on this information. The Quality Analyst automated execution and database linkage produces near-real-time results.
The system is so efficient that generating the final PDF reports is now the only rate-limiting step. They have had to build a three-second buffer because of a system time lag required to produce the PDF document. However, adding those three seconds to the reporting process has been a small price to pay compared to the weeks it previously took to generate the internal and customer documents.
All laboratory data enters the Oracle database, and the continuing project is integrating production equipment data into the database. Machine measurement integration is rapidly leading to real-time, on-line process control. Since most failures develop gradually, using SPC detects trends long before they become problems. The engineers can predict vacuum pump and purification trap failures months before an out-of-specification excursion occurs.
The Praxair Kingman staff has integrated cylinder-valve torque machines for valve-thread failure detection and next plans to integrate the vacuum pumps into the SPC system. Additional steps to identify and add more monitoring points and continued system expansion are planned, to provide pathways for preventative maintenance and effective predictive failure mode analysis.
Control limits are also maintained in the database. If data from either the lab or production floor is out of control, it is flagged when it goes into the database and a quality exception report is automatically generated. Everything, including data charts to support root-cause analysis, is automated, which eliminates the variation of having the staff manually enter these parameters. Flags are now automatically generated from the database. Automating this process removed data-entry errors.
This data management and analytic capability enables Praxair to successfully answer customer inquiries. As chemist Doug Smith says, “He who has the best data wins. We have years of supplier product and calibration data, and when questions arise, we have the support we need to back up our processes.” Additionally, SPC techniques are used to evaluate incoming materials. The analytical software allows Praxair to have data-driven discussions with suppliers on apparent out-of-control conditions (shifts, trends, etc.) Process capability and control are now the primary shipping criteria, not simply whether they meet specifications when they ship. Praxair’s management practice is to have a quarterly review of both product and process.
Praxair maintains several six sigma black and green belts to lead continuing process improvement. The SPC analytics from Quality Analyst are often what triggers a six sigma project when the results show process drift, yield problems or the need for improved product purity.
Major Process Improvement and Cost Savings
The broad-based adoption of Quality Analyst software and process-improvement methodologies has improved both profitability and customer relations. By just automating general reports and queries, Praxair has recaptured the equivalent of one Quality Manager salary and overhead which can now be applied to process and product improvement. This is in addition to process savings, customer quality awards and ratings, and the cost savings from having no customer rejects in the past four years.
The continuous-process improvement helps retain customers and is a key value Praxair provides to its customers. For many customers SPC and CPI performance are now part of the purchasing agreement.
The ongoing customer communications process uses web meetings, email, and teleconferences to review the process data and analytics to look for improvement possibilities and set new performance goals. Audits are now used as an opportunity for process improvement.
This system has worked flawlessly, with absolutely no downtime in four-and-a-half years. Even low levels of impurities can be a big problem in the electronics industry and it is paramount that Praxair’s process gas quality meets the industry’s roadmap as chips get smaller and specifications tighter.
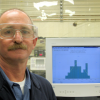